Chemical Raw Materials
Inorganic Chemistry
- Inorganic Salt
- Inorganic Base
- Inorganic Acid
- Oxides and Peroxides
- Graphene
- Silica Gel
- Metal Ore
- Coating Material
- Other
Chemical Reagents
- Organic Reagent
- Silane Reagent
- Chiral Chemical Reagents
- Grignard Reagent
- Fluorine Reagent
- Deuterium Reagent
- Other
Pesticide Raw Materials
- Herbicide
- Insecticide
- Fungicide
- Plant Growth Regulator
- Pesticide Intermediates
- Feed Additives
- Food Additives
Daily Chemicals
Hazardous Chemicals
Phone: 86-13209521394
Mail: sales27@interlgroup.com
Add: Room 305 , 3/F , Haipai Decoration Office Building , Yudu Avenue , Yuncheng , Shanxi
Factory Supply Acrylic acid Liquid CAS 79-10-7 Raw Materials
Product Overview:
Acrylic acid Liquid is the simplest unsaturated carboxylic acid with a molecular structure consisting of a vinyl group and a carboxyl group. Pure acrylic acid is a colorless, clear liquid with a characteristic pungent odor. Density 1.0511. melting point 14°C. boiling point 140.9°C. Boiling point 140.9℃. Acrylic acid Liquid is corrosive. Soluble in water, ethanol and ether. Chemical properties are active. Easily polymerized into transparent white powder. Generate propionic acid when reducing. When added with hydrochloric acid, 2-chloropropionic acid is generated, Acrylic acid CAS 79-10-7 is used in the preparation of acrylic resins, etc. It is also used in other organic synthesis. Obtained by oxidation of acrolein or hydrolysis of acrylonitrile, also synthesized from acetylene, carbon monoxide and water, or produced by oxidation of ethylene and carbon monoxide under pressure.
Acrylic acid CAS 79-10-7 is an important raw material for organic synthesis and synthetic resin monomer, is a very fast polymerization of ethylene monomer. Pure acrylic acid is a colorless clarified liquid with characteristic irritating odor. It is miscible with water, alcohols, ethers and chloroform, and is prepared from propylene obtained from oil refineries. Most Acrylic acid Raw Materials are used to manufacture acrylic esters such as methyl, ethyl, butyl, and hydroxyethyl acrylate.
Factory Supply Acrylic acid Liquid CAS 79-10-7 Raw Materials Attributes
MF:C3H4O2
MW: 72.06
EINECS:201-177-9
Specification:Acrylic acid Liquid
Sample:Acrylic acid Liquid
Brand: Acrylic acid Liquid
Appearance: White Liquid
Storage: Cool Dry Place
Brand: Globalchemical
Shelf Life: 2 Years
Test Method: HPLC
Factory Supply Acrylic acid Liquid CAS 79-10-7 Raw Materials Details
Uses and synthesis of Acrylic acid Liquid
Acrylic acid Liquid is the simplest unsaturated carboxylic acid with a molecular structure consisting of a vinyl group and a carboxyl group. Pure acrylic acid is a colorless, clear liquid with a characteristic pungent odor. Density 1.0511. melting point 14°C. boiling point 140.9°C. Boiling point 140.9°C. Strong acidity. Corrosive. Soluble in water, ethanol and ether. Chemical property is active. Easily polymerized into transparent white powder. Acrylic acid Liquid and hydrochloric acid addition to generate 2-chloropropionic acid, Acrylic acid Raw Materials used in the preparation of acrylic resins, etc., but also for other organic synthesis. It is obtained by oxidation of acrolein or hydrolysis of acrylonitrile, and can also be synthesized from acetylene, carbon monoxide and water, or oxidized from ethylene and carbon monoxide under pressure.
Acrylic acid Raw Materials is an important organic synthesis raw material and synthetic resin monomer, is a very fast polymerization of ethylene monomer. It is the simplest unsaturated carboxylic acid, consisting of a vinyl group and a carboxyl group. Pure acrylic acid is a colorless, clear liquid with a characteristic pungent odor.Acrylic acid CAS 79-10-7 is miscible with water, alcohols, ethers, and chloroform, and is prepared from propylene obtained from oil refineries. Most of them are used to manufacture acrylic esters such as methyl acrylate, ethyl acrylate, butyl acrylate, hydroxyethyl acrylate and so on. Acrylic acid and acrylic esters can be homopolymerized and copolymerized, and their polymers are used in synthetic resins, synthetic fibers, high-absorbent resins, building materials, coatings, and other industrial sectors.Occupational standards for Acrylic acid CAS 79-10-7 are TLV-TWA 6 mg/m3; TWA 30 mg/m3. The Hazardous Substances Data for Acrylic Acid is 79-10-7 (Hazardous Substances Data).
Applications / Functions of Acrylic acid Liquid
- 1, Acrylic acid CAS 79-10-7 important organic synthetic raw materials and synthetic resin monomer, is the polymerization speed is very fast ethylene monomer. Mostly used in the manufacture of acrylic acid methyl ester, ethyl ester, butyl ester, hydroxyethyl ester and other acrylic esters. Acrylic acid and acrylic ester can be homopolymerized and copolymerized, can also be copolymerized with acrylonitrile, styrene, butadiene, vinyl chloride and maleic anhydride and other monomers. Their polymers are used in synthetic resins, adhesives, synthetic rubber, synthetic fibers, highly absorbent resins, pharmaceuticals, leather, textiles, chemical fibers, building materials, water treatment, petroleum extraction, coatings and other industrial sectors. Acrylic acid is one of the important raw materials of water-soluble polymers, and starch graft copolymerization can be produced super strong water-absorbent agent.
- 2、Acrylic acid Liquid through homopolymerization or copolymerization to prepare polymers for coatings, adhesives, solid resins, molded plastics and so on.
- 3、Preparation of acrylic resin, rubber synthesis, coating preparation, pharmaceutical industry.
- 4、Warp sizing materialBy acrylic acid, methyl acrylate, ethyl acrylate, acrylonitrile, ammonium polyacrylate and other raw materials prepared by the warp sizing material, than the capacity of polyvinyl alcohol sizing material desizing, saving starch.
- 5、AdhesiveAcrylic acid Liquid, methyl acrylate, ethyl acrylate, acrylic acid-2-ethylhexyl ester copolymerization latex, can be used for electrostatic flocking, flocking adhesive, its firmness and feel good.
- 6、Water thickenerAcrylic acid Liquid and ethyl acrylate copolymer made of high molecular weight powder. It can be used as thickening agent, used in oilfield, each ton of product can increase the production of 500t of crude oil, and it has better effect on oil recovery of old wells.Adhesive with acrylic acid, methyl acrylate, ethyl acrylate, acrylic acid-2-ethylhexyl ester and so on.
- 7、Copper coating agent Acrylic acid Liquid with acrylic acid, acrylic acid, butyl acrylate, acrylic acid - 2 - ethylhexyl ester, styrene and other tetramer copolymer latex for coated paper, color retention does not yellow, printing performance is good, do not stick to the roller, better than the styrene-butadiene latex can be saved dry coolant.
- 8、Polyacrylic acid salts Acrylic acid CAS 79-10-7 use of acrylic acid can produce a variety of polyacrylic acid salt products (such as ammonium salt, sodium salt, potassium salt, aluminum salt, nickel salt, etc.). Used as coagulant, water quality treatment agent, dispersant, thickener, food preservative acid and alkali resistant desiccant, softener and other polymer additives.
Acrylic acid Liquid properties and stability
Acrylic acid Liquid colorless liquid with irritating odor. Soluble in water, ethanol and ether.
Acrylic acid Liquid undergoes the characteristic reactions of carboxylic acids and reacts with alcohols to give the corresponding esters. The most common acrylic esters include methyl acrylate, butyl acrylate, ethyl acrylate, and 2-ethylhexyl acrylate.Acrylic acid CAS 79-10-7 and its esters, either by themselves or by mixing with other monomers, will undergo polymerization to form homopolymers or copolymers. Monomers commonly copolymerized with acrylic acid include amides, acrylonitrile, vinyl-containing, styrene, and butadiene. These polymers are used in the production of a variety of plastics, coatings, adhesives, elastomers, floor polishes and paints.
- Acrylic acid Raw Materials flammable, its vapor and air can form explosive mixtures, in the presence of open flame, high heat can cause combustion and explosion. It can react strongly with oxidizer. In case of high heat, polymerization reaction can occur, releasing a large amount of heat and causing container rupture and explosion. When encountering heat, light, moisture, peroxide and iron, it is easy to self-polymerization and cause explosion.
- Acrylic acid Liquid has double bond and carboxyl functional group joint reaction, can occur addition reaction, functional group reaction and ester exchange reaction, long preparation of polycyclic and heterocyclic compounds, easy to be reduced to propionic acid by hydrogen, can be decomposed into formic acid and acetic acid in contact with alkali.
- Acrylic acid Raw Materials has strong acidity. Corrosive. Chemical property is active. Easily polymerized into transparent white powder. Generate propionic acid when reducing. 2-Chloropropionic acid is produced when it is added with hydrochloric acid.Acrylic acid CAS 79-10-7 can have the characteristic reaction of carboxylic acid, and the corresponding ester can be obtained when it is reacted with alcohol. Acrylic acid and its esters polymerize on their own or in combination with other monomers to form homopolymers or copolymers. Monomers commonly copolymerized with Acrylic Acid Raw Materials include amides, acrylonitrile, vinyl-containing, styrene, and butadiene. These polymers are used in the production of various plastics, coatings, adhesives, elastomers, floor polishes and paints.
- Acrylic acid CAS 79-10-7 has strong corrosiveness, medium toxicity. Its aqueous solution or high concentration of vapor will irritate the skin and mucous membranes. The oral LD50 for rats is 590mg/kg. pay attention not to contact with acrylic acid solution or steam, wear good working clothes and cap, protective glasses and rubber gloves when operating. Production equipment should be airtight. Work and storage places should have good ventilation.
Production method of Acrylic acid Liquid
- Acrylonitrile hydrolysis method: acrylonitrile is first hydrolyzed with sulfuric acid to generate sulfate of acrylamide, and then hydrolyzed to generate acrylic acid, by-product of ammonium bisulfate. This method has been greatly developed in Rohm and Haas Company in the United States. The first step of hydrolysis temperature is 90~100℃. To acrylonitrile in a slightly excessive amount of 55% ~ 85% of sulfuric acid, 1h after acrylonitrile that is completely transformed; then add water for the second hydrolysis, and will be raised to 125 ~ 135 ℃; hydrolysis products by distillation under reduced pressure and acrylic acid. This method is actually a development of the early cyanoethanol method. Due to the by-product acid ammonium sulfate generated after hydrolysis is difficult to handle, the price of raw material acrylonitrile is more expensive, thus affecting the production cost.
- Cyanoethanol method: this method uses chloroethanol and sodium cyanide as raw materials, the reaction generates cyanoethanol, which is hydrolyzed in the presence of sulfuric acid at 175 ℃ to generate acrylic acid: if the hydrolysis reaction is carried out in methanol, it generates methyl acrylate; 3. β -propiolactone: this method is actually a development of the early cyanoethanol method.
- β - propiolactone method: the raw material for this method is vinyl ketone, so it is also known as the vinyl ketone method, the reaction is as follows: first of all, the acetic acid cleavage to vinyl ketone, and then with the anhydrous formaldehyde reaction to generate β - propiolactone; used as a catalyst in the 140 ~ 180 ° C, 2.5 ~ 25MPa, propolactone and then contact with hot 100% phosphoric acid, isomerized to acrylic acid. With β - propiolactone method for the production of acrylic acid, product purity, yield is also higher, by-products and unreacted materials can be recycled, and is suitable for continuous production, but it needs to use acetic acid as a raw material, especially because of propiolactone is considered to be a carcinogen, so this method has not been adopted in the industry.
- High-pressure Reppe method: acetylene dissolved in tetrahydrofuran, in the presence of a catalyst consisting of nickel bromide and copper bromide, reacted with carbon monoxide and water to produce acrylic acid. This method is characterized by: the use of tetrahydrofuran as a solvent, can reduce the danger of high-pressure treatment of acetylene; at the same time, the catalyst is not used in the original Rape method of nickel carbonyl, only nickel salt. Propylene mixed with air and water vapor according to a certain molar ratio, in the presence of molybdenum - bismuth and other composite catalysts, the reaction temperature of 310-470 ℃, atmospheric pressure oxidation to produce acrolein, yield of 90%. And then the acrolein and air and water vapor mixed at a certain molar ratio, in the presence of molybdenum - vanadium and other composite catalysts, the reaction temperature of 300-470 ℃, atmospheric pressure oxidation to produce acrylic acid, yield up to 98%. This method is divided into one-step and two-step method. One-step method is propylene oxidized in a reactor to generate acrylic acid; two-step method is propylene oxidized in the first reactor to generate acrolein, acrolein and then into the second reactor oxidation to generate acrylic acid. Two-step method according to the reactor structure, but also divided into fixed bed and fluidized bed method. Acrylic acid industrial production methods, cyanoethanol method, high-pressure Repe method has been basically eliminated, previously used as raw material for the cleavage of acetic acid to vinyl ketone, and then react with anhydrous formaldehyde to generate propiolactone, and then contact with hot phosphoric acid isomerization for acrylic acid. Called vinyl ketone method or β-propiolactone method is also basically eliminated, acrylonitrile method is only used in a few old devices. The main industrial use is the modified Reppe method and propylene oxidation method, and the latter is more common and most promising. In the patent report, there is also the production method of propionic acid as raw material.
- propylene oxidation: propylene and air and water vapor mixed at a certain molar ratio, in the presence of molybdenum-bismuth composite catalyst, oxidation of acrolein, and then acrolein and air and water vapor mixed at a certain molar ratio, in the presence of molybdenum-vanadium-tungsten composite catalyst, oxidation of acrylic acid. According to the structure of the reactor, this method is divided into two kinds of fixed-bed method and fluidized bed method. In addition to the U.S. Sohio method using fluidized bed, the other are used in the fixed-tube bed.
- ① Fixed bed method. The method is: the first reactor feed propylene content of 4% ~ 7%, 20% ~ 50% water vapor, the rest is air, air speed 1300 ~ 2600h-1, reaction temperature 320 ~ 340 ℃, pressure 0.1 ~ 0.3MPa; the second reactor air speed of 1800 ~ 3600h-1, reaction temperature 280 ~ 300 ℃, pressure 0.1 ~ 0.2MPa, propylene and The conversion of acrolein is above 95%, and the selectivity of acrylic acid is 85%~90% in terms of propylene. The process is as follows: propylene, water vapor and preheated air are mixed into the first reactor. Propylene is oxidized to acrolein. Then it enters the second reactor to get acrylic acid. The first and second reactors are tube reactors, using molten salt as heat carrier, and the reaction gas from the second reactor enters the rapid cooling tower after heat exchange with the raw air, and the water added at the top of the tower is inversely contacted, so as to obtain an aqueous acrylic acid solution with a content of 20%~30%. The aqueous solution enters the extraction tower, and butyl acetate or xylene is used as the extractant to separate the water from the acrylic acid. The water-rich extraction solution comes out from the top of the extraction tower and enters the solvent recovery tower, where the extractant is vaporized from the top of the tower and sent back to the extraction tower for recycling. Wastewater is discharged at the bottom of the tower. The residual liquid in the extraction tower goes to the solvent distillation tower. The solvent (extractant) is evaporated from the top of the tower and sent back to the extraction tower for recycling; crude acrylic acid is obtained at the bottom of the tower, and then acrylic acid products are obtained after removing light components and heavy components. Propylene by gas-phase contact oxidation reaction to make acrylic acid process, in addition to the product acrylic acid, there are traces of acrolein, acetic acid, pentanone acid, anthranilic acid, as well as other aldehydes impurities. Aldehydes are oxidized by-products of propylene or generated due to the oxidation of impurities contained in the raw material of propylene, such as acetaldehyde, formaldehyde, benzaldehyde, furfural, acrolein, etc. The reaction gas containing these by-products remains in the acrylic acid product after cooling, extraction and distillation. Using conventional methods of refining acrylic acid products, still contains about (50~500) × 10-6 of aldehyde material. In order to adapt to the needs of high-purity acrylic acid, Beijing Oriental Chemical Plant to the plant's polymerization of acrylic acid as raw materials, developed a method for the preparation of high-purity acrylic acid, so that the total aldehyde content of less than 5 × 10-6, to meet or exceed the data requirements of the relevant foreign literature (foreign less than 10 × 10-6). The experimental method is: add a certain amount of polymerization grade acrylic acid to the flask, add the reagent DL, under atmospheric pressure after 10 ~ 80 ℃ range of treatment, and then into the packed tower to deal with distillation, the temperature in the tower kettle 60 ~ 80 ℃, the temperature at the top of the tower is 50 ~ 70 ℃, the vacuum is 93.33 ~ 99.99 KPa, the use of supplemental polymerization blocking agent and gas-phase blocking agent method, which prevents the distillation of acrylic acid in the process of distillation. Polymerization. Distillate collected by this method is high-purity acrylic acid;
- ② Fluidized bed method② Fluidized bed method. Method is propylene, air, water through the first boiling bed reactor to generate acrolein, and then into the second boiling bed reactor to generate acrylic acid, and then sprayed, cooled, extracted distillation, and then in the decompression tower to remove acetic acid and acrylic acid. The ratio of the oxidizing mixture is propylene:air:water=1:12:8 (molar ratio). The temperature of the first boiling bed reactor is 370℃, and the contact time is 2s; the temperature of the second boiling bed reactor is 260℃, and the contact time is 2.25s. The conversion rate of propylene is 75%~80%, the total yield is 40%, the content of acrylic acid is 97%, and the average content is 93%. Domestic in the first reactor using seven components (molybdenum-vanadium-phosphorus-iron-cobalt-nickel-potassium) catalyst, propylene oxidation of acrolein; in the second reactor using three components (molybdenum-vanadium-tungsten) catalyst, acrolein oxidation of acrylic acid, when the propylene: air:water = 1:10:6, the contact time of 5.5s, the linear velocity of 0.6m / s reaction temperature: a section of 370-390 ℃, 270-300 ℃, the second section of 270-300 ℃, the reaction temperature of 2.6 m / s reaction temperature: a period of 370-390 ℃, 270-300 ℃, the second section of 270-300 ℃, the average content of 93%. When the reaction temperature is 370-390 ℃ for one stage and 270-300 ℃ for the second stage, the conversion rate of propylene in the first stage is 78.7%-87% and the yield of acrolein is 51.9%-57.2%, the conversion rate of propylene in the second stage is 79.3%-89.4% and the yield of acrylic acid is 48.3%-49.8%, and the air-time yield of acrylic acid is 55-60 kg/(m3catalyst-h).
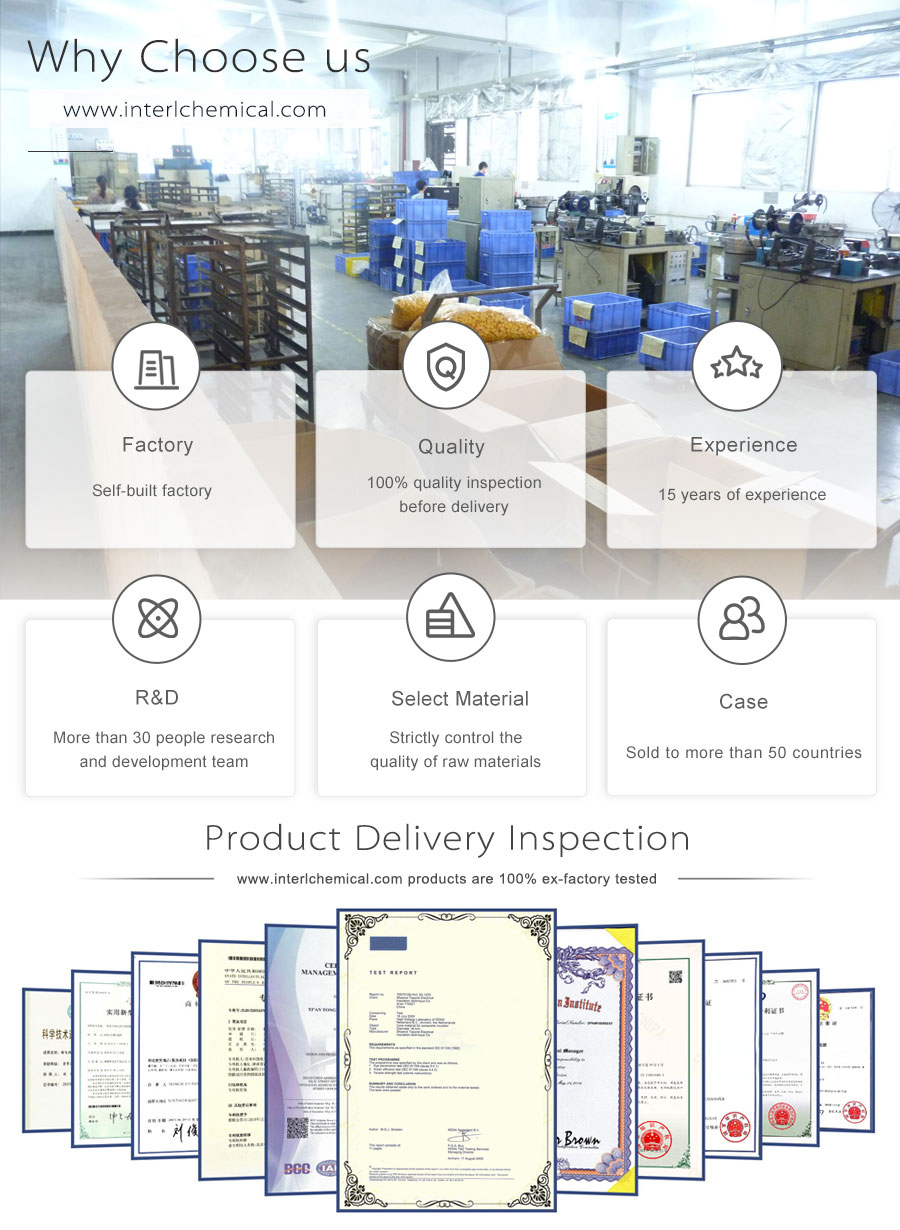
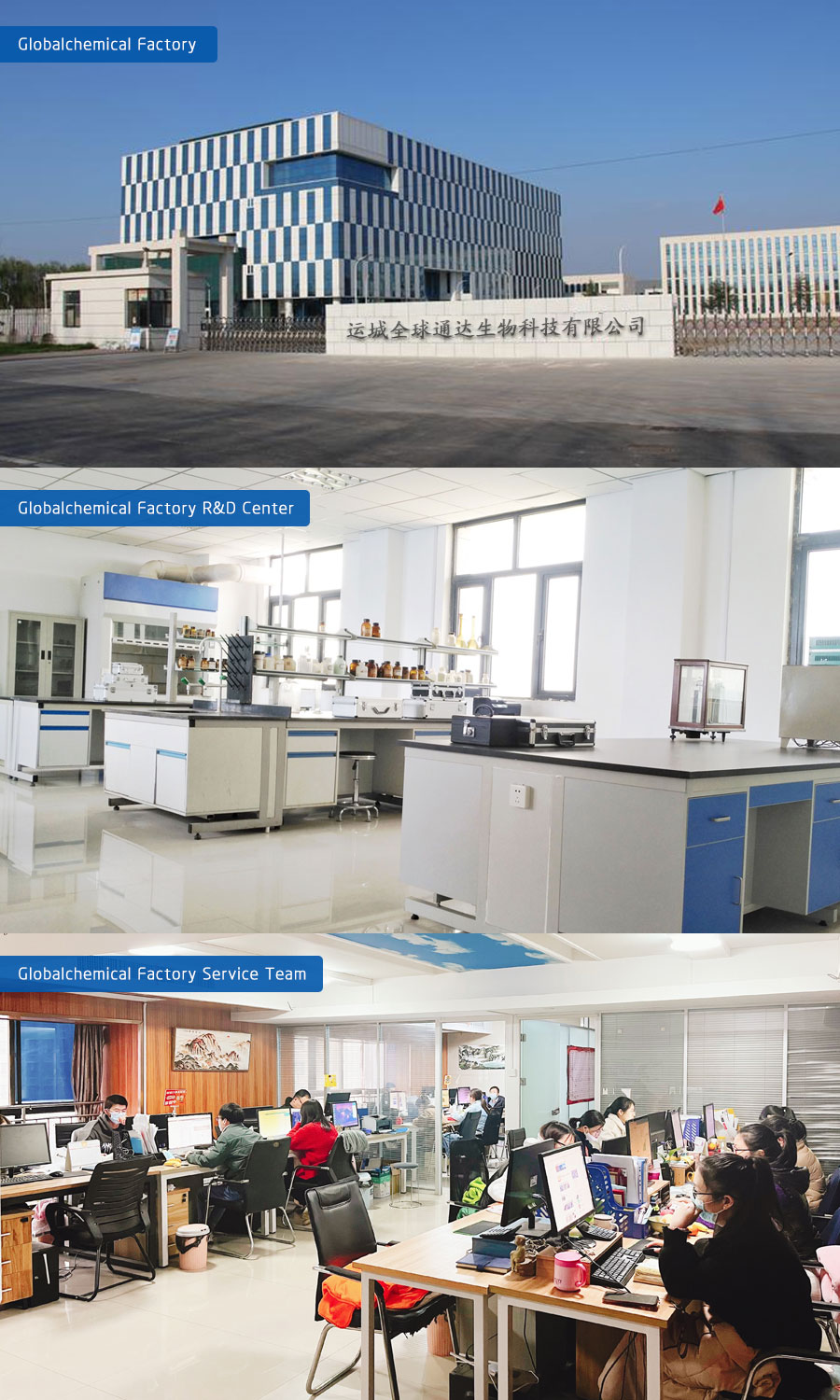
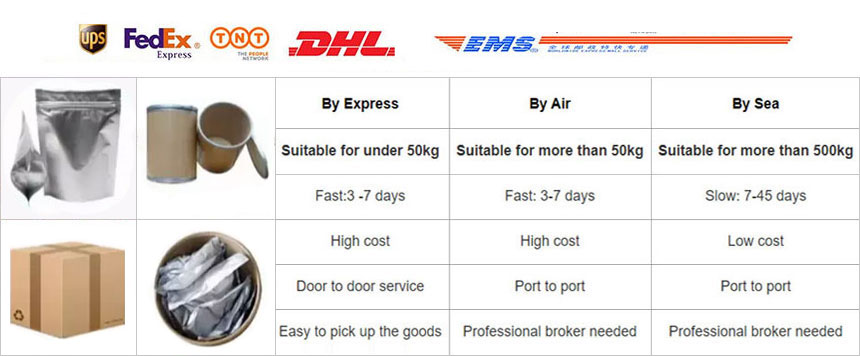